
The frame builder's prime directive for making a faster bike is to ensure that every iota of pedalling power is transferred as efficiently as possible to the drive-train. Dialing up torsional rigidity is a key consideration in this regard. By carefully manipulating the attributes of material, geometry, tube diameter and wall thickness, the custom builder can maximize side-to-side stiffness while maintaining desirability in other aspects of the ride (comfort, handling, etc.).
GURU takes power transfer to another level by designing shapely, custom carbon frames that take full advantage of this material's exceptional properties and by rigorously testing all of our frames to optimize torsional stiffness:
Advanced Modelling – Carbon
"Carbon fiber is pretty amazing stuff," says GURU founder and resident science officer, Tony Giannascoli. "As an anisotropic material, it can be made to exhibit different properties based on its orientation. On the flipside, composites and sharp radii just don't get along." In the traditional & ‘cut & bonded’ method of making a carbon bike, the sharp radius sections featured at the intersection of tubes represent an inherent weakness as they are particularly susceptible to stress risers that compromise the integrity of the frame. This vulnerability is typically overcome through over-building at the joint level, which negatively limits fine-tuning possibilities, adds unnecessary weight and "deadens" the ride.
To fully capitalize on the performance characteristics offered by carbon fiber technology, you essentially need to create fluid transitions (at the joints) and shapes that maximize volume exactly where it's needed. GURU's engineering crew spends countless hours modelling designs and lay-up configurations to perfect this aspect. The following video excerpts exemplify this work as they show finite element analysis results for two distinct carbon lay-up configurations:
- an early generation Geneo;
- a newly optimized version (2009 model).
Load Testing
In developing our frame designs, we also take the time to perform a specific protocol of static deflection tests that measure relative stiffness in key areas of the frame. The goal is to optimize stiffness levels (ie. degree, direction, plane) that correspond to desired performance characteristics (as identified by our road testers). These load tests are also performed once models go into production to ensure consistent performance levels from unit-to-unit.
To illustrate, the following enumerates relative torsional rigidity levels for our most popular titanium road frames:
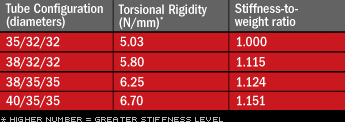
None of the above is inherently better than the others. It's all a question of matching up the right performance attributes to the individual cyclist.
The Power of a Perfect Fit
Every human body is unique; every cyclist has their own set of preferences and objectives. Ergo, every individual rider corresponds to a particular set of coordinates on a bike where their biomechanics are optimized in relation to aerodynamics, stability and sustainability. Based on the thousands upon thousands of bike builds we have successfully executed (for an endless spectrum of individuals), GURU has developed a superior expertise on what it takes to release a person's full power on a bicycle. In conjunction with the best fitters in the industry, we work to pinpoint the "soul" of each cyclist and build a corresponding machine that can completely unleash it.
Part science, part art, this body of knowledge continues to grow with every single frame we make.